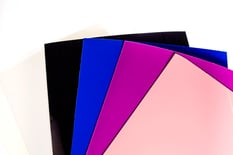
One of the wonderful, but confusing, things about PP is that there are several different grades of the same polymer and no two resins behave alike. One one hand, this is great because it gives us the opportunity to tailor the plastic sheet formulation to our customers application; but on the other hand, this can lead to confusion regarding which grade of PP is best suited for which application. So what is the difference? To offer some guidance, we put together a basic guide to help you differentiate between the three main grades of PP. Continue reading to learn more!
PP is a semi-crystalline polymer that is hazy in its natural state due to the presence of crystals. PP is generally characterized as having a higher stiffness at a lower density, resistance to higher temperatures, and an excellent strength to weight ratio. The three main grades of PP resin allow for improvement of specific properties as determined by the composition of the polymer chain:
Homopolymer PP can be considered the most ‘basic’ grade of PP resin. This grade of PP resin is more rigid and has good resistance to high temperatures, making it particularly suitable for high-heat applications such as hot fill and microwave applications or steam sterilization applications. However, the tradeoff to this is lower impact resistance, particularly at low temperatures. For this reason homopolymer resins are not recommended for freezer applications or other applications where the material will undergo extremely low temperatures for an extended period of time.
Additional characteristics of this grade of PP resin include a high melting point leading to excellent stiffness, superior scratch resistance, and good chemical resistance against most inorganic acids, alkalis and salts. In addition, this grade of PP resin provides strong resistance to environmental stress cracking when in contact with alcohols, esters, detergents or polar hydrocarbons. Homopolymer resins can be clarified through the use of additives as exemplified by Impact’s UltraClear polypropylene sheet.
Check out our blog post to learn more facts about PP!
Random Copolymer Polypropylene
Random copolymer PP resins are created by modifying the polymer chain through the addition of random chains of ethylene among the PP units. Due to the presence of ethylene, the rigidity characteristic of homopolymer resins is somewhat sacrificed, however, this results in improved impact strength and a softer feel. Additional benefits to this include improved heat sealability, lower melting point, resistance to environmental stress cracking and improved clarity. Random Copolymer PP resins also exhibit good chemical resistance against most inorganic acids, alkalis and salts. Clarified grades of random copolymer are available from Impact Plastics.
Impact Copolymer Polypropylene (or Block Copolymer PP)
Si
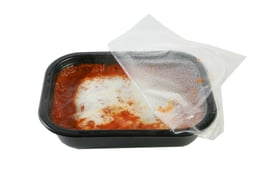
Download our 903D Clarified Impact Copolymer PP Data Sheet to learn more!
A new class of its own, Impact Plastics' sister brand, ICPG, has developed a specialty portfolio of polypropylene solutions called XPP. Designed to offer a drop-in solution for PS replacement in form-fill-seal food, medical and pharmaceutical packaging applications, XPP offers improvements to key functional properties in the form of a more sustainable and recyclable product including:
- Optimized performance with enhanced oxygen & moisture barrier protection before use of EVOH
- Controlled cost, improved efficiencies & increased output vs PS & PET alternatives
- Maintains key packaging function of current PS solutions - including "snap-ability"
- Improved sustainability & recyclability using RIC #5
- Compliant with Proposition 65 guidelines
- Compatible with existing FFS equipment & processes for drop-in PS replacement
Download the XPP Product Sheet to learn more!
As with every application, the end goal for the packaging application will guide your decision making when it comes to what grade of PP to use. Homopolymer PP resins can withstand high heat and exhibit excellent stiffness, but the tradeoff is impact strength; random copolymers offer improvements to impact strength but have a lower melting point; and block copolymer PP resins offer increased impact strength at very low temperatures as well as high heat resistance.
With continued advancements in technology, both on the resin production side and the extrusion side, traditional differences in the primary grades of PP resin have blurred. Impact Plastics recommends testing of the material for every new application and custom tailors PP formulations to meet the customers ultimate goals for their project.
To learn more about the grades of PP available from Impact Plastics, download Impact's PP data sheets today!