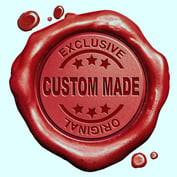
Static is not only annoying but when it comes to plastic, the presence of static can lead to issues such as increased handling problems, excessive dust and dirt build up on the surface of the plastic part, parts sticking, damage of sensitive medical or electronic products and even fire or explosion hazard if static sparks are formed near flammable liquids. The addition of anti-static additives help to reduce static electric charges either by making the material conductive, or interacting with moisture in the atmosphere, forming a microscopic layer of water on the surface of the material. Anti-static additives are available as both internal and external additives.
Impact Plastics has the capability to impart anti-static properties to the material using either an internal or an external anti-static additive. Internal anti-static additives that can be incorporated and blended into the polymer at the extrusion level. During this process the additive is blended homogeneously with the polymer to provide the much-needed surface resistivity required for electronics packaging. As the material cools, the additive migrates to the surface and begins to pick up moisture from the surrounding environment. External anti-static coatings can be applied to the sheet formulation using our customizable roller-coater capabilities.
CaCO3 is one of the most widely used mineral fillers in the plastics industry, and its use in rigid packaging has increased significantly over the years. The addition of calcium carbonate to polypropylene sheet has been shown to improve the performance of several properties including improvements to heat deflection temperature, increased impact strength, stiffness and barrier properties. The use of CaCO3 in materials such as polypropylene can also help streamline processing by allowing the plastic to heat and cool down faster and reduce shrinkage by improving the heat deflection of the material.
For more information on the benefits of using CaCO3 check out our blog post!
Similarly to CaCO3 filler, the use of Talc in polypropylene sheet helps to remedy several common challenges of thermoforming polypropylene while enhancing several properties of the polymer. The use of talc in polypropylene sheet has been shown to improve the performance of several properties including increased rigidity, resistance to heat, increased heat deflection, faster cooling and reduced shrinkage.
Unlike calcium carbonate, however, the addition of talc results in a significant decrease in impact strength, so if high impact strength is an important specification, CaCO3 is the better choice.
For more information on deciding between calcium carbonate and talc click here!
Polypropylene is a semi-crystalline polymer which gives the material a hazy appearance in its natural state. Polypropylene normally crystallizes slowly, forming collections of large and complex crystals or spherulites. Without the addition of a clarifying additive, the size of the spherulites grow to be larger than the wavelength of visible light, resulting in light scattering and hazing the material.
The addition of the clarifying agent increases the rate of crystallization throughout the polymer. Because there are more crystals packed into the same space, the crystals grow smaller, allowing for light transmission and enhanced clarity. So now you can take advantage of all of the wonderful characteristics inherent to PP while still achieving a part with the visual appeal desired by today’s consumers. To learn more visit Milliken Chemical.
The appearance of fog seen on the surface of clear plastic packaging is the result of the condensation of water vapor on the surface of the material. In food packaging, this cannot only ruin the shelf appeal of the product by preventing the consumer from seeing the contents, but it could also impact the quality of the food. The use of anti-fog additives work to minimize surface tension, resulting in a non-scattering film of water rather than single tiny droplets.
Impact Plastics has the capability to impart anti-fog additives to the material using either an internal or an external anti-fog additive or coating to combat this fogging effect. Internal anti-fog additives are non-ionic surfactants, or compounds that lower the surface tension between two liquids or a solid and a liquid. A degree of incompatibility exists between the polymer and the additive, and as a result, the additive migrates to the surface, decreasing the surface tension of the water droplets, and thus reducing the surface tension between the water and the surface of the plastic packaging. This allows the water to spread out creating a more uniform layer of water, thus improving the transparency of the water droplets and eliminating the fogging effect. External anti-fog coatings can be applied to the sheet formulation using our customizable roller-coater capabilities.
For more information on how you can further customize our products to meet your application's needs, contact our team today!